+86-13732282311
merlin@xcellentcomposites.com
Let the world benefit from composite materials!
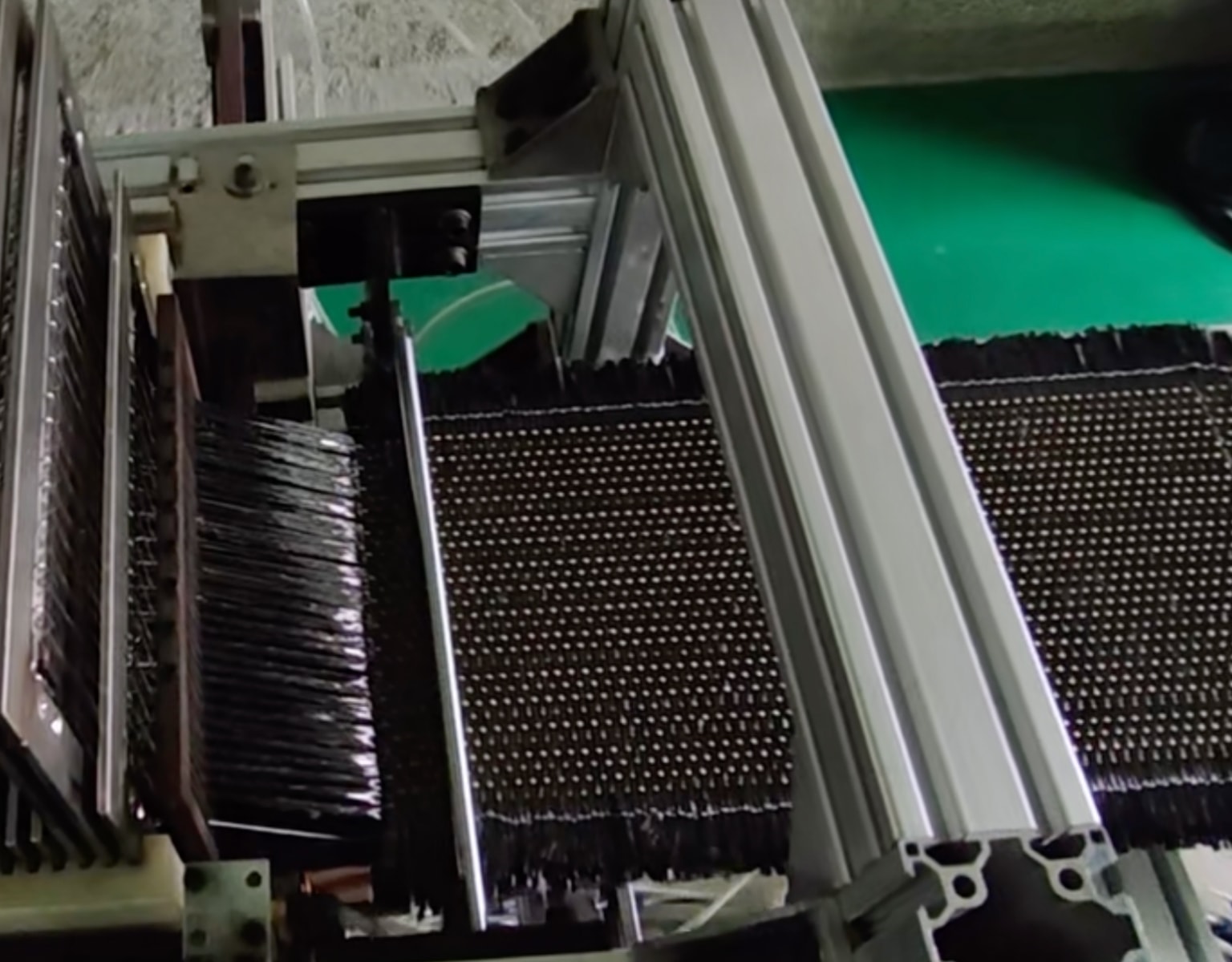
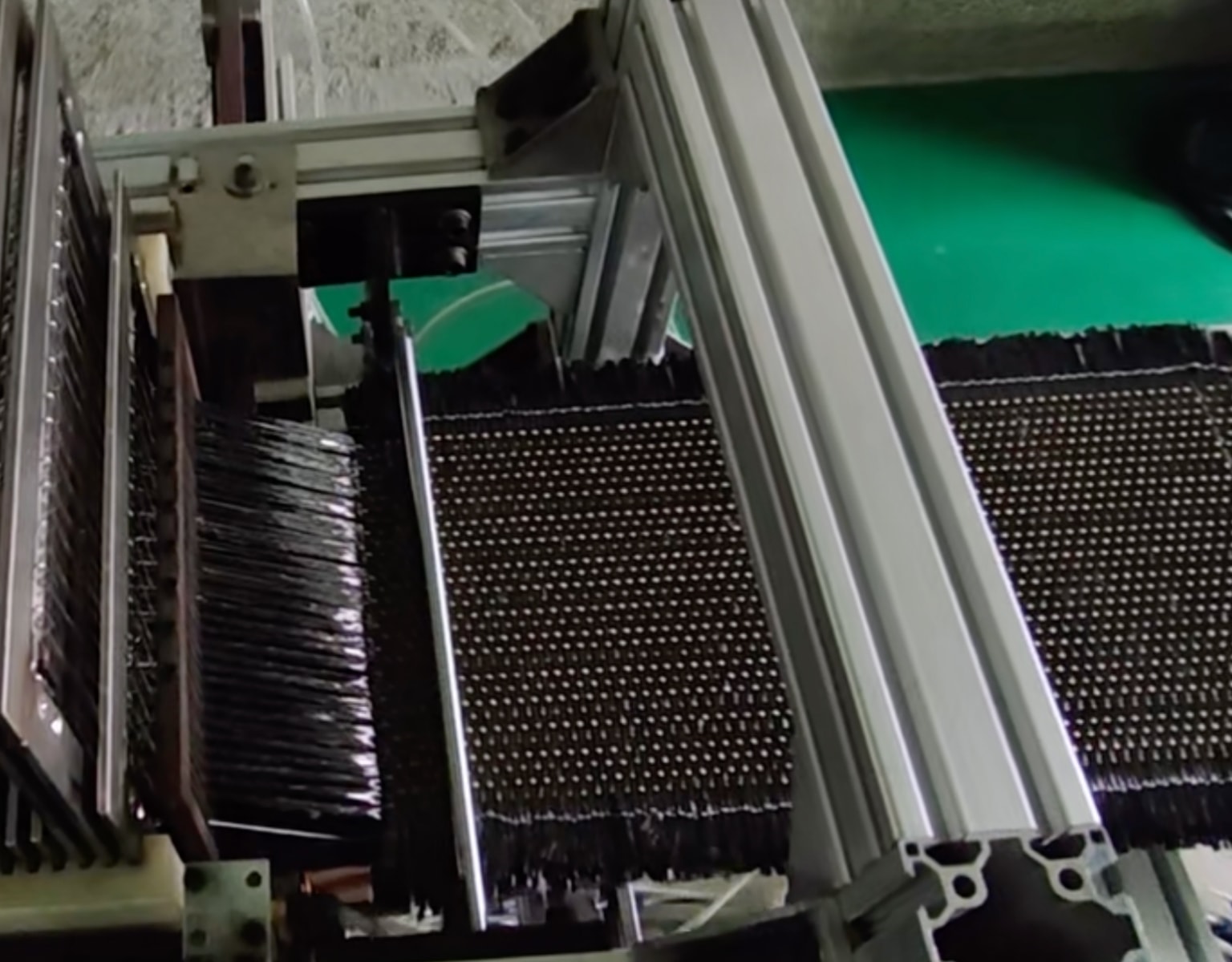
Unique Composite Fabrics
Three-Dimensional Textiles
Three-dimensional textiles employ various techniques to interlace high-performance fibers in between layers, thereby enhancing interlaminar shear strength and fracture toughness of composite materials. They have found applications in a wide array of materials, such as missile nose cones, antenna window materials, rocket engine nozzle linings, satellite truss structures, helicopter rotor blades, and aircraft brake pads.
The preparation of three-dimensional textiles typically involves the use of high-performance fibers like carbon fibers, glass fibers, silicon carbide fibers, aramid fibers, and high-strength polyethylene fibers. This variability allows for the customization of composite material performance; by selecting appropriate fibers and fabric structures based on load distribution and operational conditions of engineering structures, specific requirements can be met. By fabricating three-dimensional textiles in near-net dimensions according to the approximate contour and thickness of composite material components, known as prefabricated bodies, damages and material wastage incurred through machining, connections, and assembly are reduced. This, in turn, further enhances the overall integrity and quality of component structures.
Three-dimensional textiles manifest as fiber or sheet materials in a three-dimensional form. Fibers are interwoven in different structural configurations to create three-dimensional textiles, such as orthogonal triaxial fabrics and three-dimensional weaves. By using fibers to connect stacked layers of two-dimensional sheets, stitched fabrics, fine piercing fabrics, needled fabrics, and Z-pinned fabrics can be formed. The multitude of forms in three-dimensional textile processes significantly influences the performance and manufacturing efficiency of composite materials. Compared to two-dimensional textiles, the primary advantage of three-dimensional textiles lies in their ability to enhance interlaminar properties of composite materials, as they include various forms of interlayer connecting fibers within their structure.
Stitched Structures
In the 1980s, the application of stitched composite materials emerged. Through multiple experiments, it was observed that the tensile strength at stitched areas exceeded that of non-stitched areas by over 70%. In comparison to two-dimensional laminate panels, three-dimensional stitched composite materials exhibit advantages such as simpler fabrication methods, lower costs, enhanced impact damage resistance, and higher damage tolerance. However, the stitching process may lead to a loss of in-plane fibers, consequently decreasing in-plane stiffness and strength. Moreover, the equipment for stitched structure fabrication is costly, and the dimensions of sewn components are limited by the width of the sewing machine, necessitating further research in this area.
Popular Composite Materials
Popular Composite Materials
Related Composite Materials Capabilities
Related Composite Materials Capabilities
Composites Knowledge Hub
Composites Knowledge Hub