+86-13732282311
merlin@xcellentcomposites.com
Let the world benefit from composite materials!
Composite materials for automotive
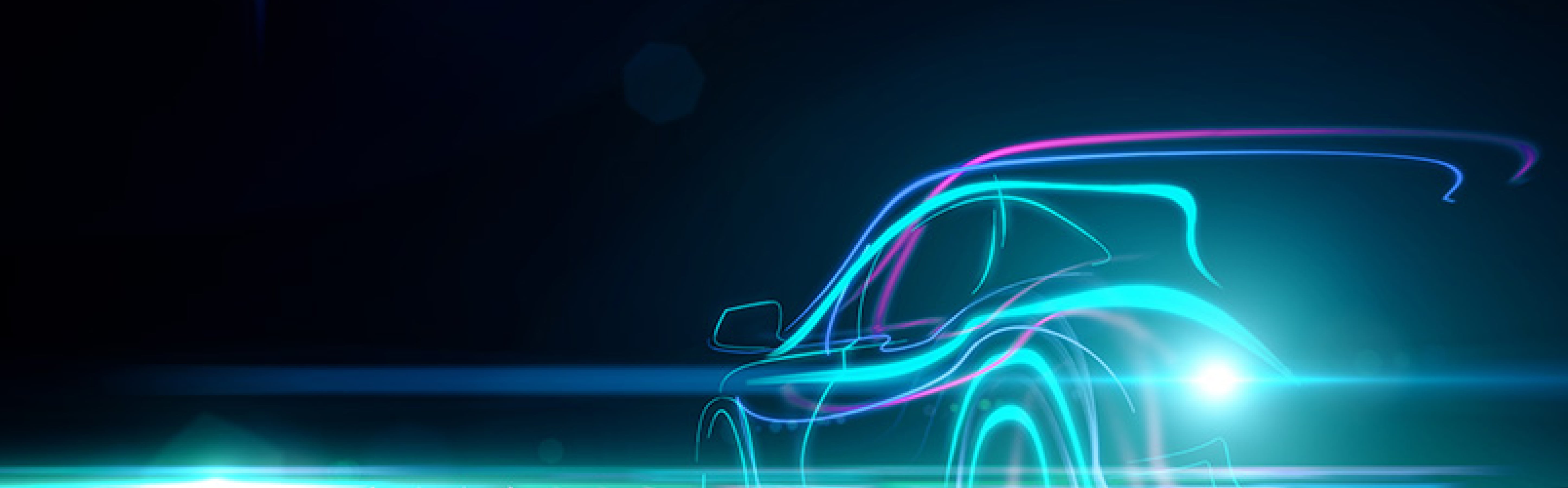
Composite materials for automotive
Automotive composite materials are revolutionizing the industry by offering lightweight, high-strength alternatives to traditional metals. Composite materials for automotive applications improve fuel efficiency, enhance safety, and reduce environmental impact. Additionally, custom carbon fiber car parts provide superior performance and aesthetics, offering tailored solutions for high-performance vehicles.
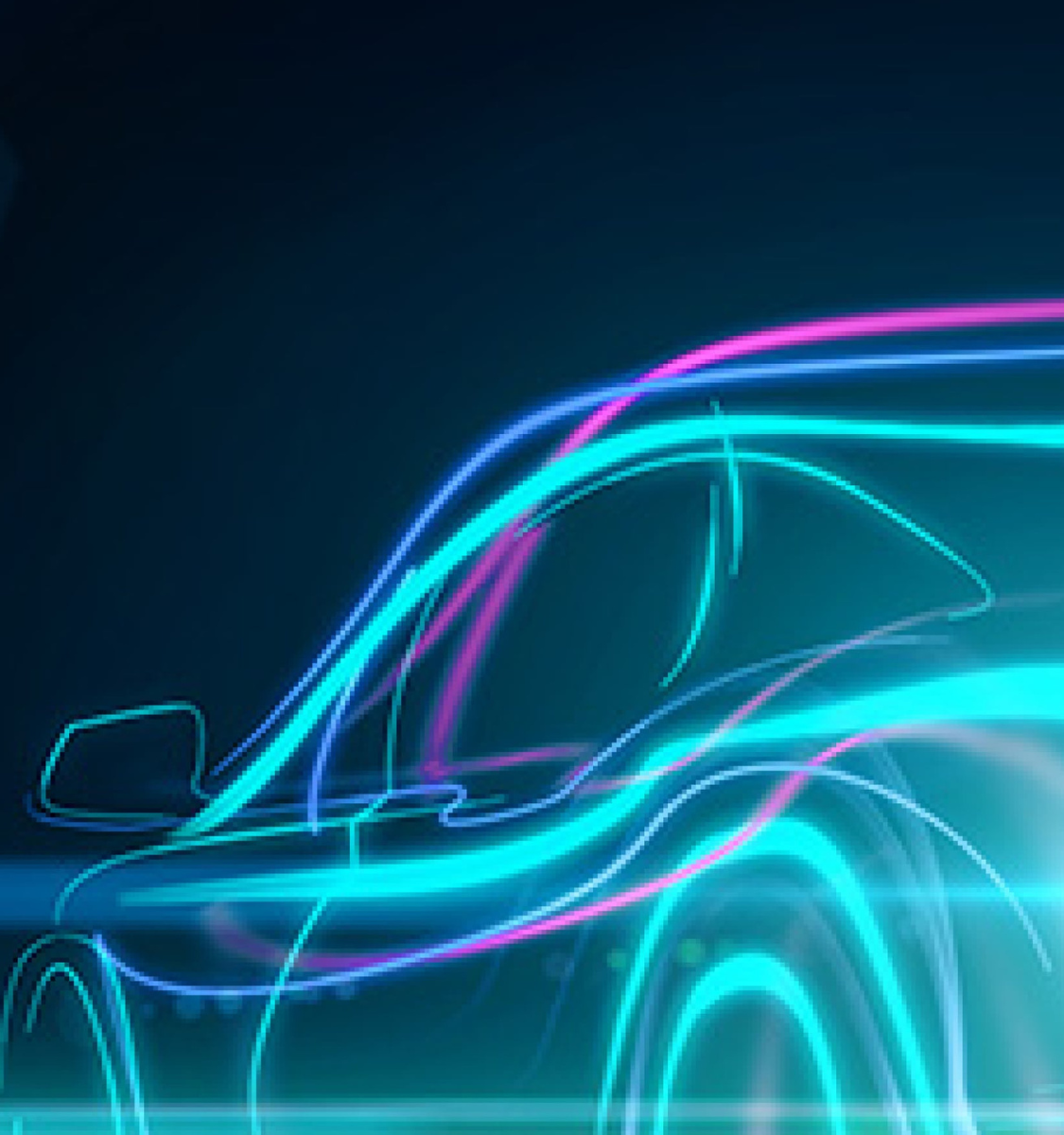
Composite materials for automotive
Automotive composite materials are revolutionizing the industry by offering lightweight, high-strength alternatives to traditional metals. Composite materials for automotive applications improve fuel efficiency, enhance safety, and reduce environmental impact. Additionally, custom carbon fiber car parts provide superior performance and aesthetics, offering tailored solutions for high-performance vehicles.
Automotive
Automotive
Composite materials have found widespread application in the automotive manufacturing sector due to their low energy consumption, convenience in processing, high performance, and extended lifespan, particularly in automotive components and interiors. They offer new solutions for vehicle lightweighting, performance enhancement, and cost control.
Composite materials have found widespread application in the automotive manufacturing sector due to their low energy consumption, convenience in processing, high performance, and extended lifespan, particularly in automotive components and interiors. They offer new solutions for vehicle lightweighting, performance enhancement, and cost control.
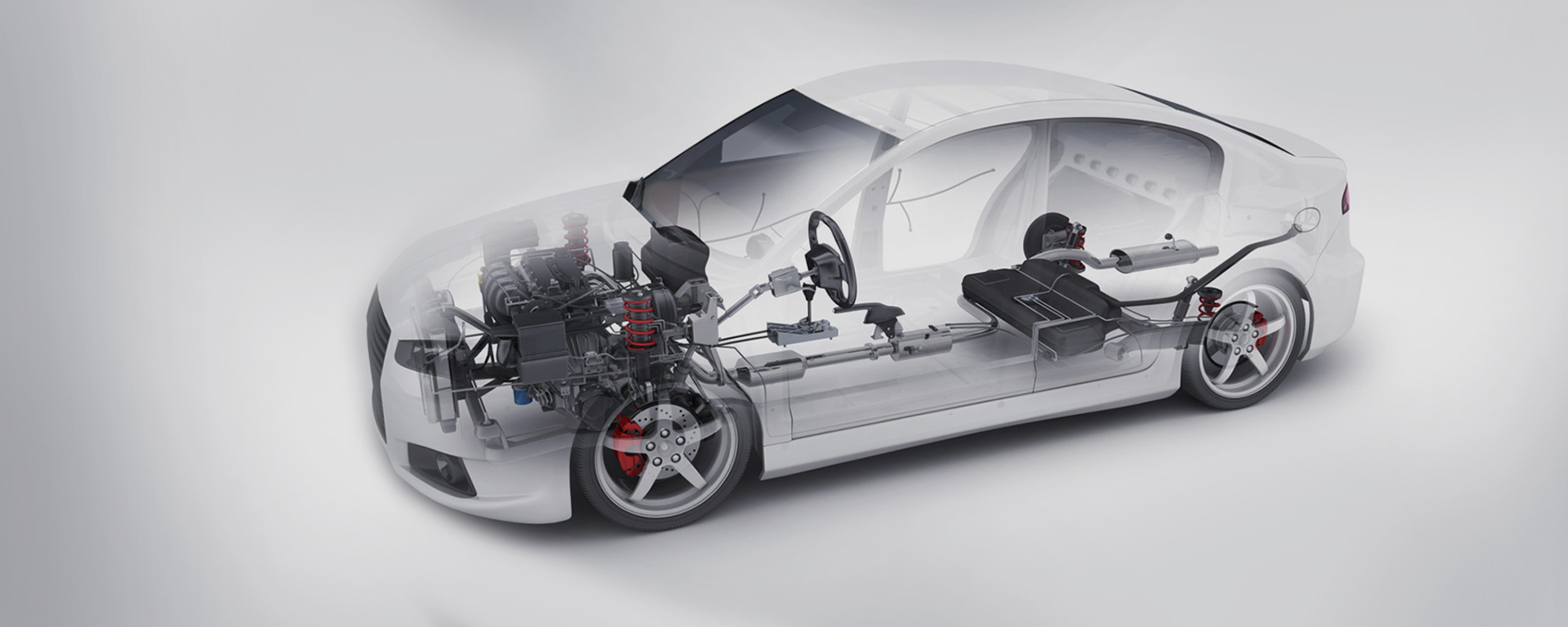
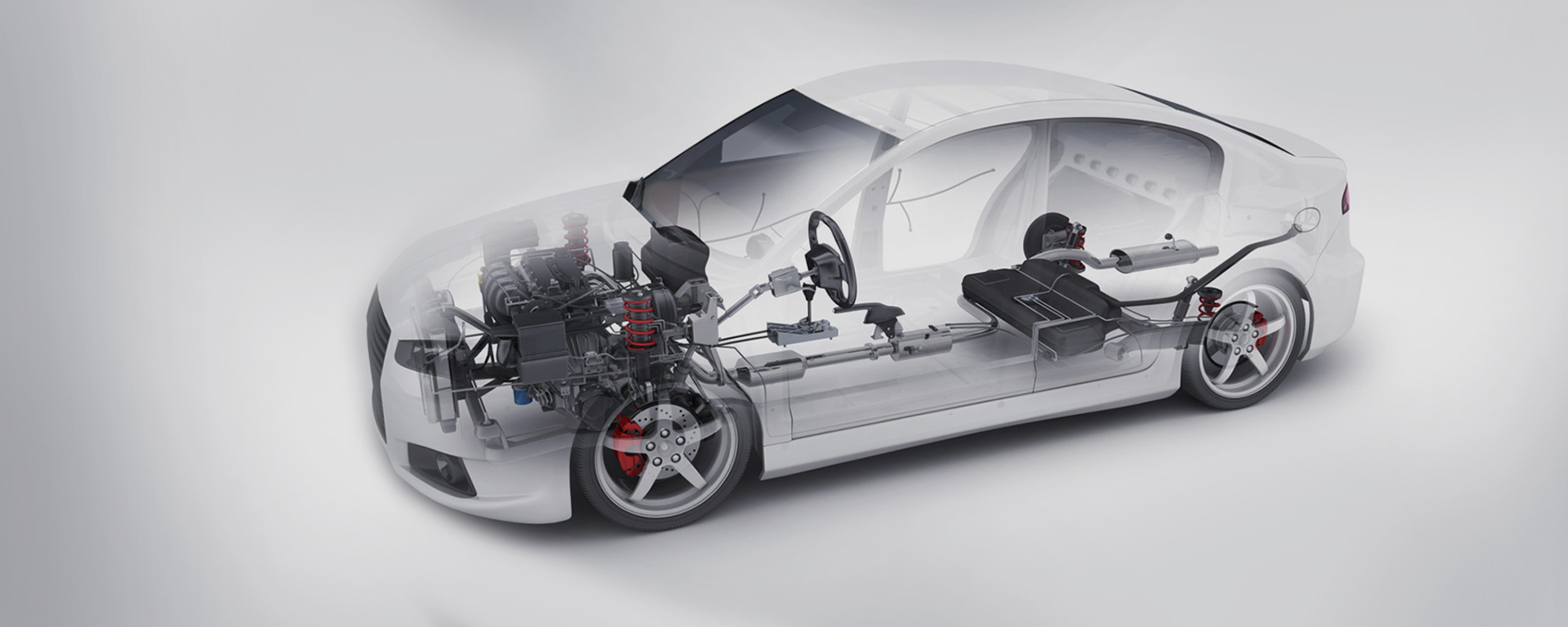
One of the primary areas where composite materials are extensively utilized in the automotive industry is in the vehicle's body structure, notably with Carbon Fiber Reinforced Plastic (CFRP). CFRP, known for its low density, high modulus, and high specific strength, is suitable for lightweighting large structural components. For instance, the CFRP passenger compartment of the BMW i3 weighs only 148 kilograms, 57.6% lighter than a traditional steel body, resulting in a reduction of approximately 200 kilograms. While the application of CFRP has extended from supercars to luxury vehicles and new energy vehicles, its use in mainstream models is constrained due to its relatively high cost.
CFRP is also widely employed in exterior body panels and interior components, particularly in high-end luxury vehicles. These panels are often offered as high-end optional packages or sport kits, including the hood, grille, and light decorative frames. There is also a market for specialized CFRP aftermarket components.
One of the primary areas where composite materials are extensively utilized in the automotive industry is in the vehicle's body structure, notably with Carbon Fiber Reinforced Plastic (CFRP). CFRP, known for its low density, high modulus, and high specific strength, is suitable for lightweighting large structural components. For instance, the CFRP passenger compartment of the BMW i3 weighs only 148 kilograms, 57.6% lighter than a traditional steel body, resulting in a reduction of approximately 200 kilograms. While the application of CFRP has extended from supercars to luxury vehicles and new energy vehicles, its use in mainstream models is constrained due to its relatively high cost.
CFRP is also widely employed in exterior body panels and interior components, particularly in high-end luxury vehicles. These panels are often offered as high-end optional packages or sport kits, including the hood, grille, and light decorative frames. There is also a market for specialized CFRP aftermarket components.
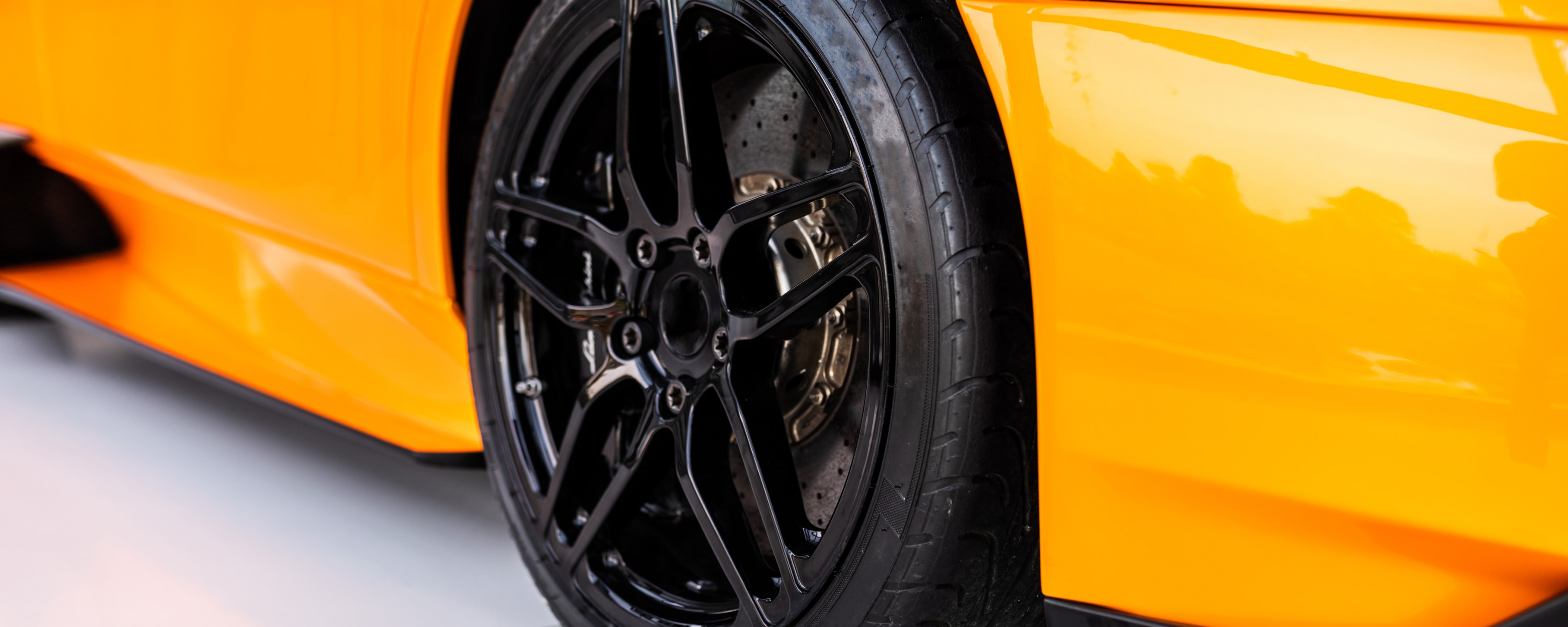
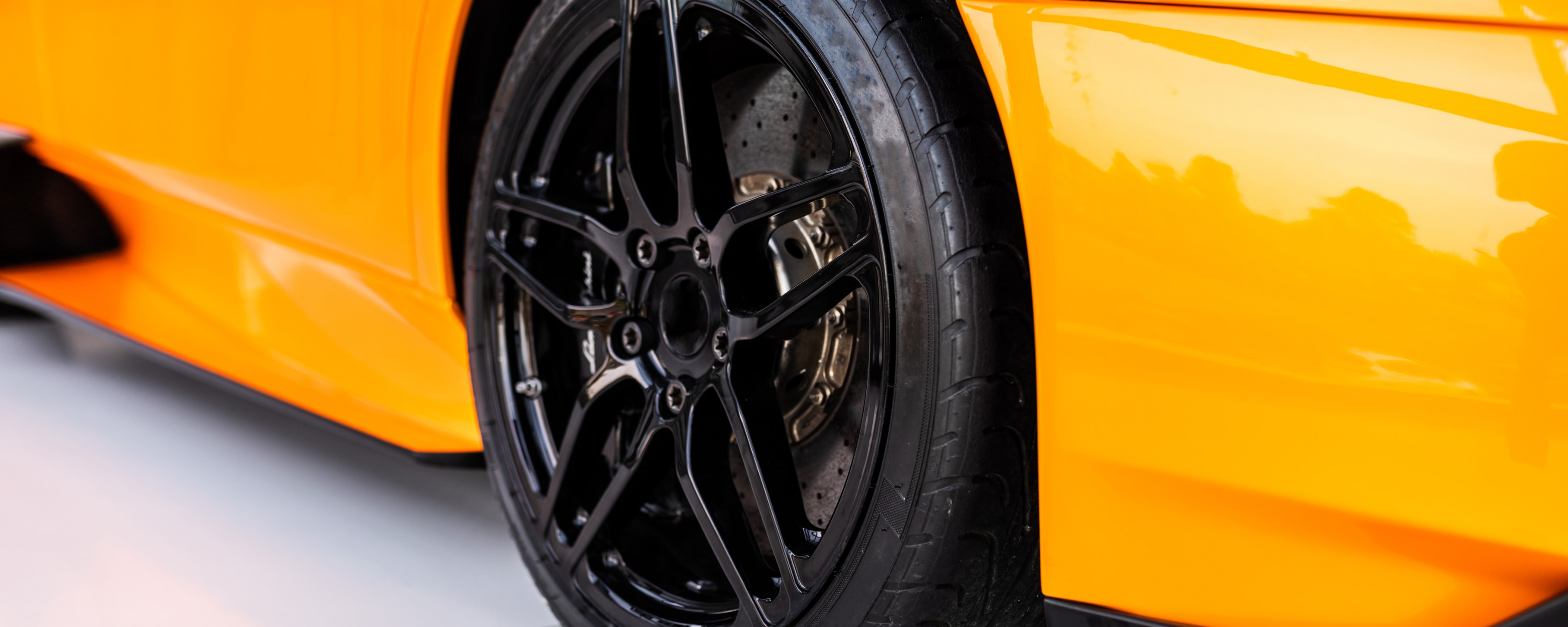
The chassis system represents another crucial area for CFRP application, despite facing greater challenges. Chassis components such as drive shafts, subframes, and control arms are under research. For example, CFRP drive shafts can significantly reduce weight while meeting high strength and fatigue requirements, enhancing vibration resistance. CFRP subframes are lighter than aluminum alloy subframes, such as the CFRP subframes developed by Ford and Magna, achieving a weight reduction of up to 34%.
The application of composite materials in the automotive industry contributes to improved vehicle performance, reduced energy consumption, and production costs, although cost remains a primary obstacle to widespread adoption. With advancements in manufacturing technology and the realization of economies of scale, it is anticipated that composite materials will play an increasingly pivotal role in future automotive manufacturing.
The chassis system represents another crucial area for CFRP application, despite facing greater challenges. Chassis components such as drive shafts, subframes, and control arms are under research. For example, CFRP drive shafts can significantly reduce weight while meeting high strength and fatigue requirements, enhancing vibration resistance. CFRP subframes are lighter than aluminum alloy subframes, such as the CFRP subframes developed by Ford and Magna, achieving a weight reduction of up to 34%.
The application of composite materials in the automotive industry contributes to improved vehicle performance, reduced energy consumption, and production costs, although cost remains a primary obstacle to widespread adoption. With advancements in manufacturing technology and the realization of economies of scale, it is anticipated that composite materials will play an increasingly pivotal role in future automotive manufacturing.
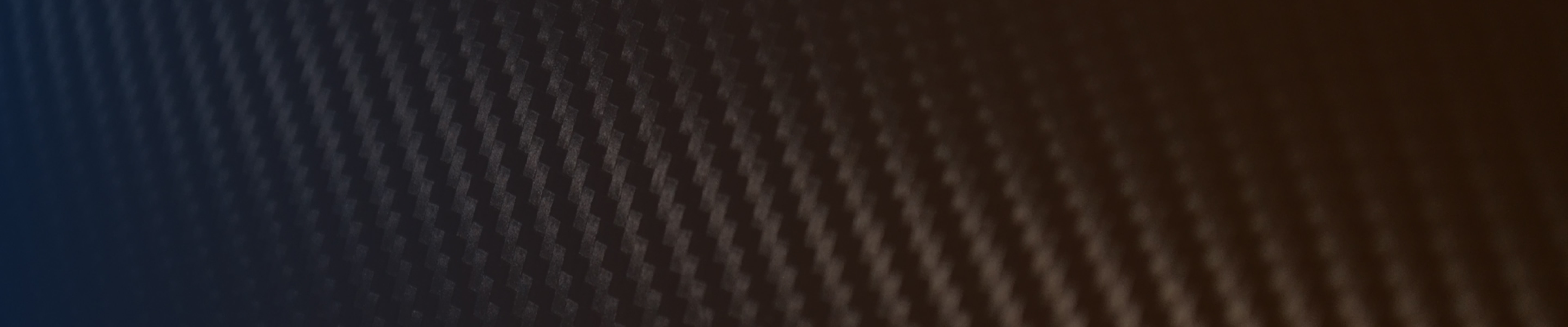
Get In Touch With Us!
To know more about our composite products and solutions, contact our experts! Here is how you can reach us.
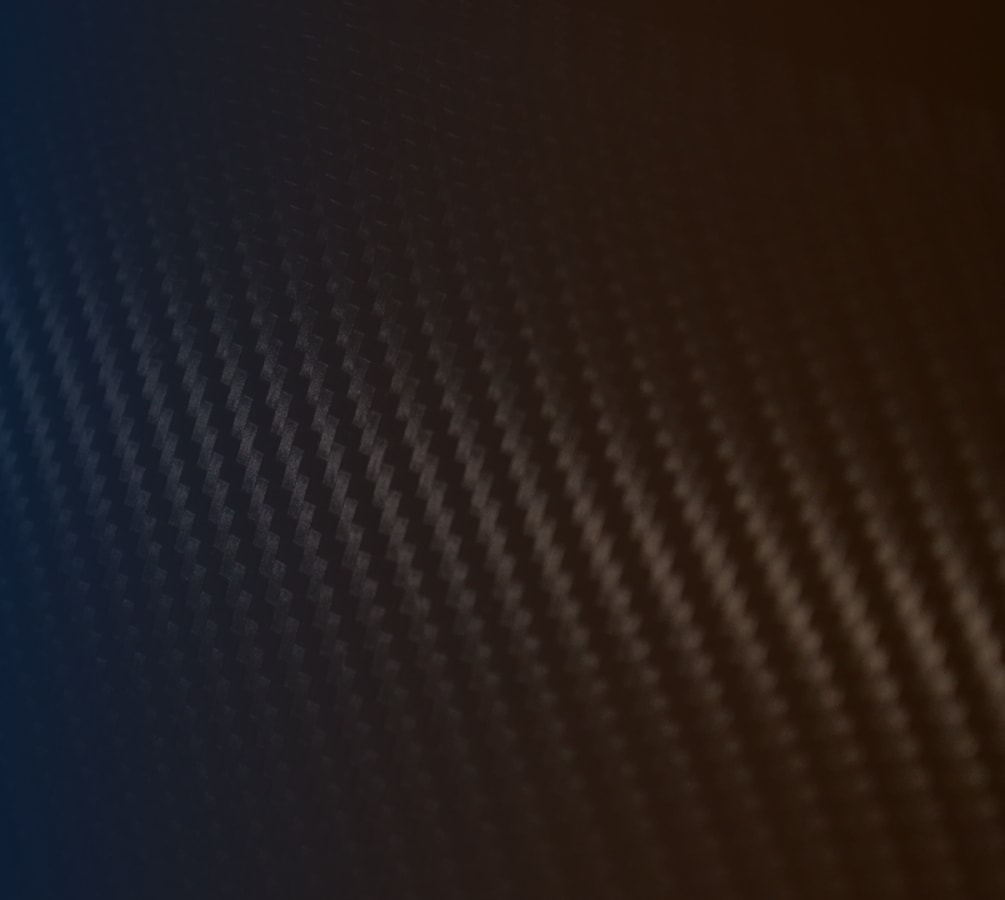
Get In Touch With Us!
To know more about our composite products and solutions, contact our experts! Here is how you can reach us.
Popular Composite Materials
Popular Composite Materials
Related Composite Materials Industries
Related Composite Materials Industries
Composites Knowledge Hub
Composites Knowledge Hub