+86-13732282311
merlin@xcellentcomposites.com
Let the world benefit from composite materials!
Composites for energy technologies
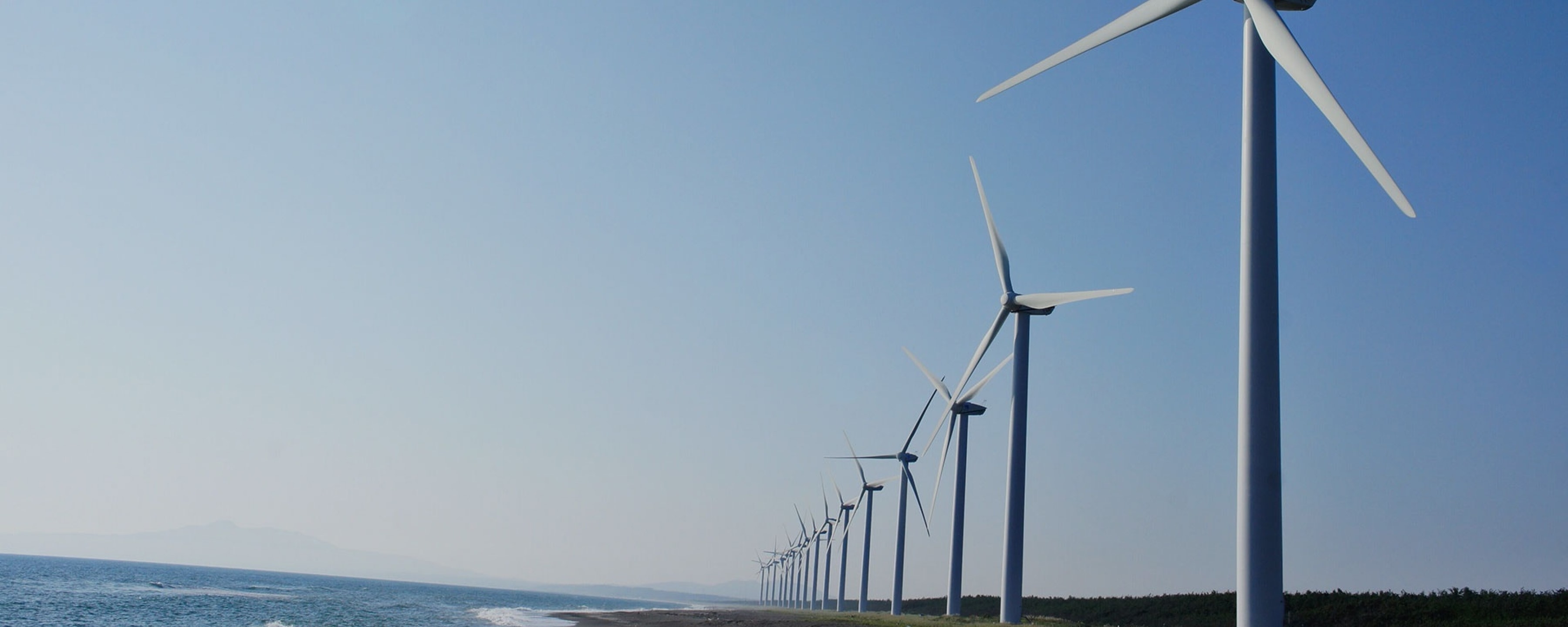
Composites for energy technologies
Composite energy technologies are transforming renewable energy with lightweight, durable materials. Carbon fiber wind turbine blades offer superior strength and efficiency, enhancing performance in high-wind conditions. Meanwhile, fiberglass wind turbine blades provide a cost-effective, corrosion-resistant solution for large-scale energy production. These innovations improve sustainability and energy output.
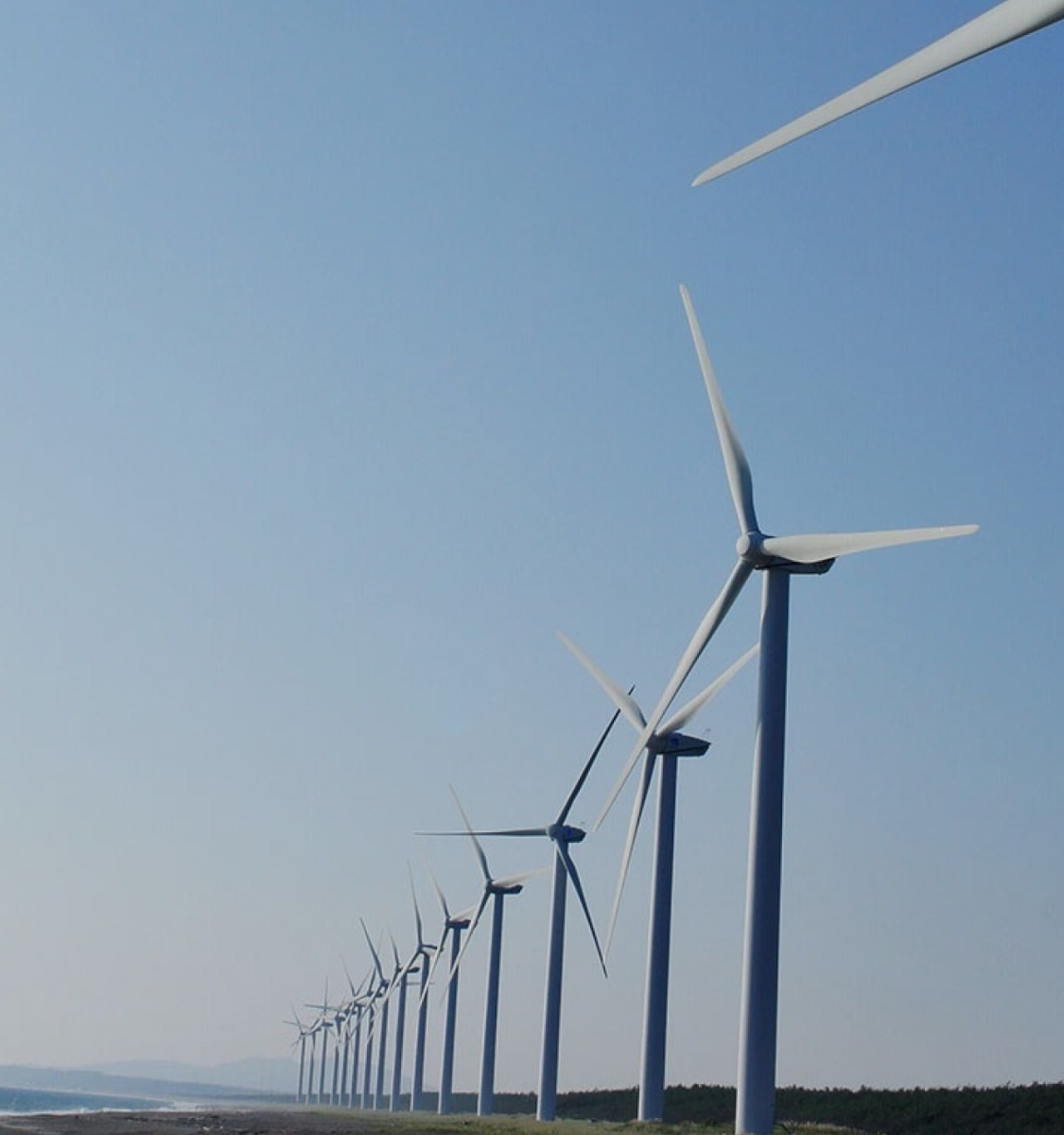
Composites for energy technologies
Composite energy technologies are transforming renewable energy with lightweight, durable materials. Carbon fiber wind turbine blades offer superior strength and efficiency, enhancing performance in high-wind conditions. Meanwhile, fiberglass wind turbine blades provide a cost-effective, corrosion-resistant solution for large-scale energy production. These innovations improve sustainability and energy output.
Wind Energy
Wind Energy
The wind energy market has long stood as one of the most extensively utilized fields for composite materials. In the early days, commercial wind farms utilized fiberglass composite blades measuring 10 to 15 meters in length. However, in modern offshore wind turbines, blade lengths have increased to 65 to 80 meters, and even longer, exemplified by the introduction of Vestas' V236-15.0 MW offshore wind turbine blades in 2021, reaching a staggering length of 115 meters. As wind turbine dimensions continue to expand, carbon fiber-reinforced materials have begun to be integrated into the main spar caps of blades to reduce weight and enhance stiffness.
The wind energy market has long stood as one of the most extensively utilized fields for composite materials. In the early days, commercial wind farms utilized fiberglass composite blades measuring 10 to 15 meters in length. However, in modern offshore wind turbines, blade lengths have increased to 65 to 80 meters, and even longer, exemplified by the introduction of Vestas' V236-15.0 MW offshore wind turbine blades in 2021, reaching a staggering length of 115 meters. As wind turbine dimensions continue to expand, carbon fiber-reinforced materials have begun to be integrated into the main spar caps of blades to reduce weight and enhance stiffness.
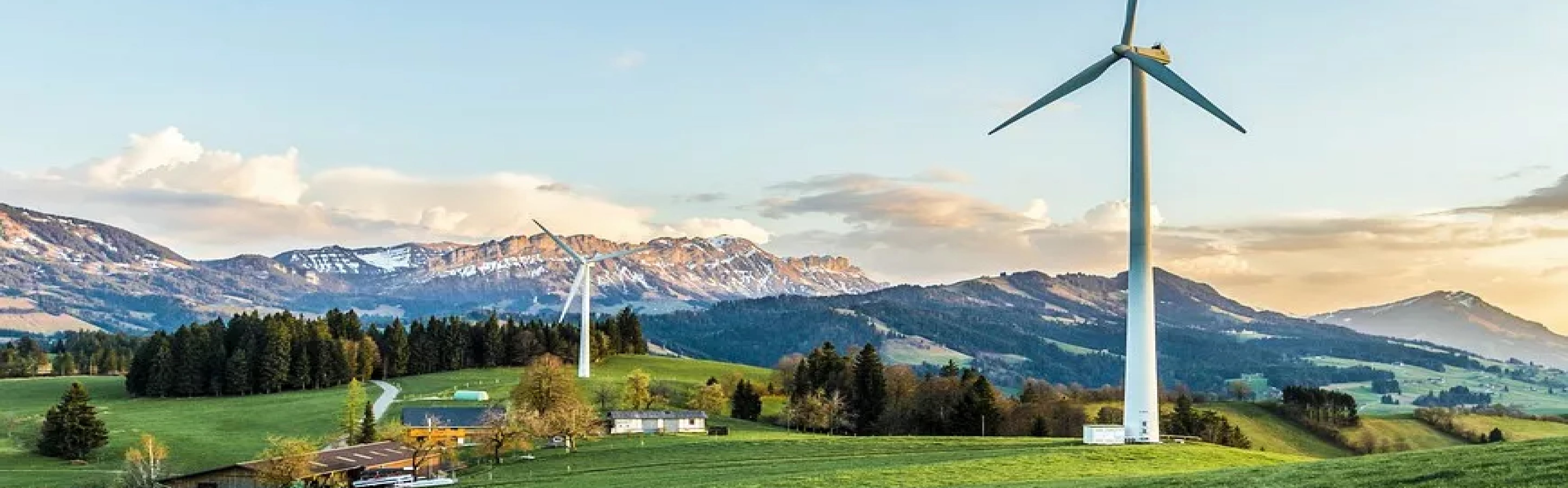
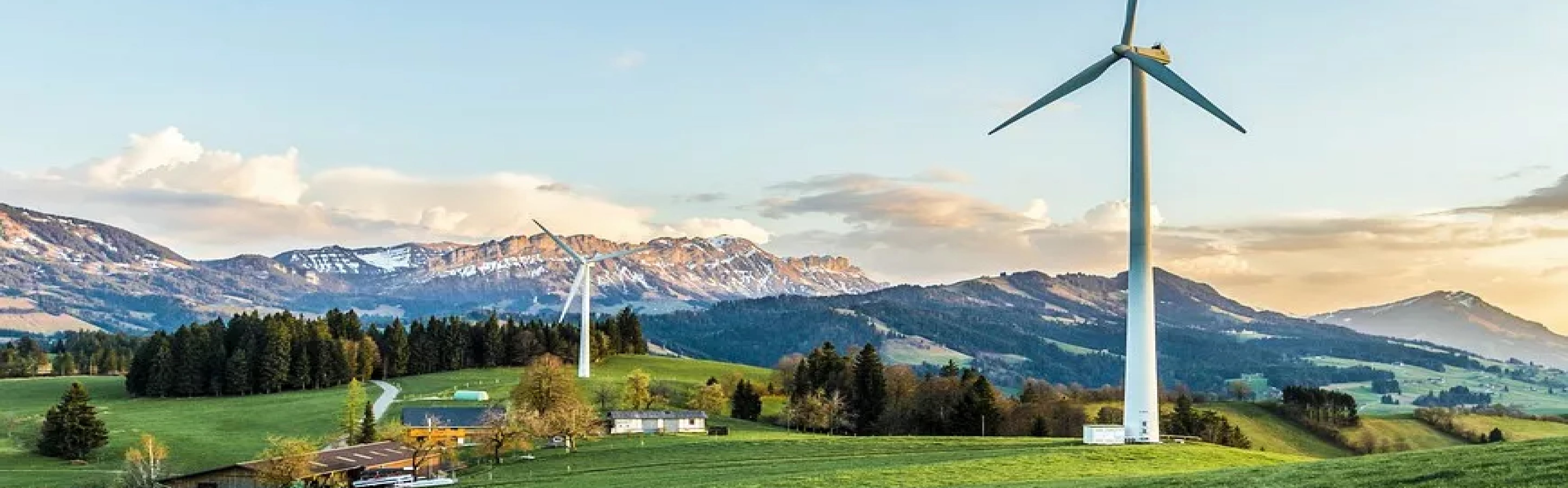
Research and development efforts in the offshore wind energy sector are actively exploring the utilization of composite materials in floating wind turbine platforms. These platforms can be installed in deep offshore areas, broadening the geographical scope of wind power generation compared to fixed foundation turbines.
Wind turbine blades serve as the most critical and cost-intensive component in wind power systems, representing 20% to 30% of the total cost. Typically crafted from fabric-reinforced composite materials, these blades offer advantages such as high strength, lightweight nature, corrosion resistance, straightforward manufacturing processes, and easy maintenance. While glass fiber is commonly used, incorporating high-performance fibers like carbon fiber and Kevlar can further enhance blade performance, albeit with some cost increment.
Research and development efforts in the offshore wind energy sector are actively exploring the utilization of composite materials in floating wind turbine platforms. These platforms can be installed in deep offshore areas, broadening the geographical scope of wind power generation compared to fixed foundation turbines.
Wind turbine blades serve as the most critical and cost-intensive component in wind power systems, representing 20% to 30% of the total cost. Typically crafted from fabric-reinforced composite materials, these blades offer advantages such as high strength, lightweight nature, corrosion resistance, straightforward manufacturing processes, and easy maintenance. While glass fiber is commonly used, incorporating high-performance fibers like carbon fiber and Kevlar can further enhance blade performance, albeit with some cost increment.
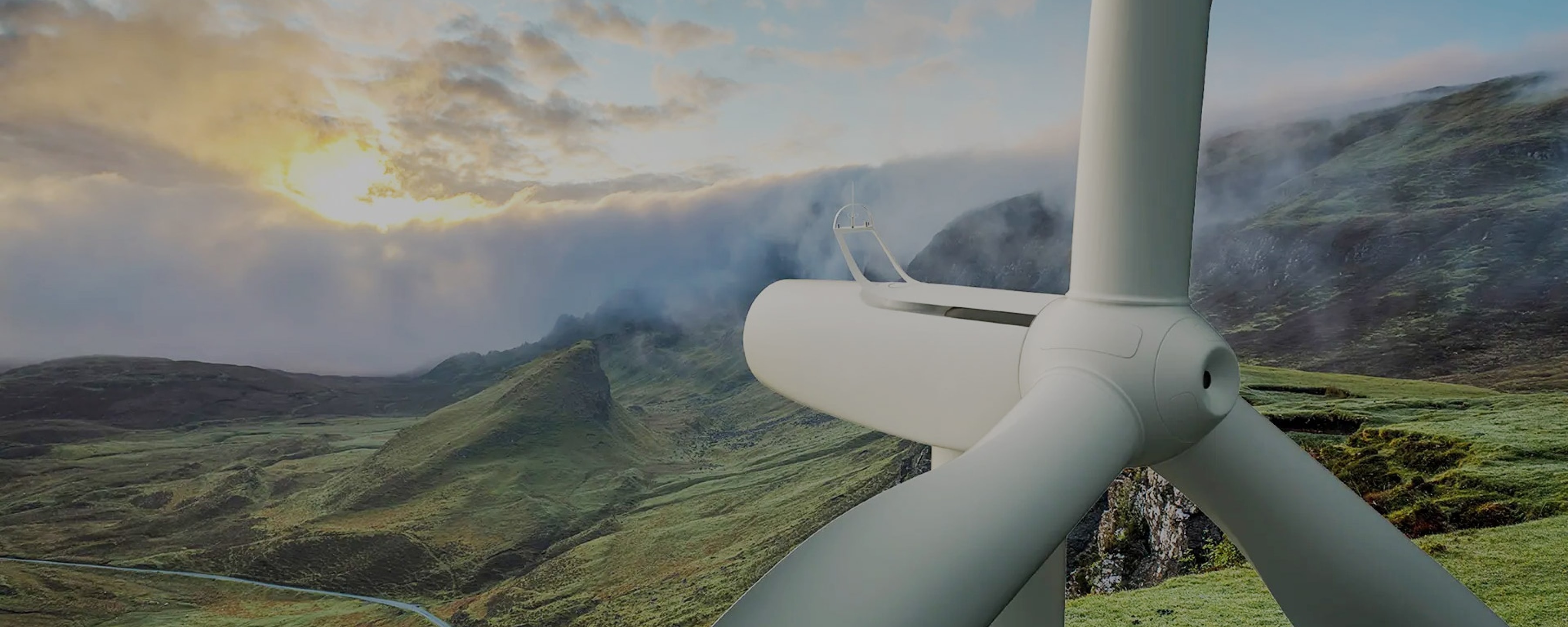
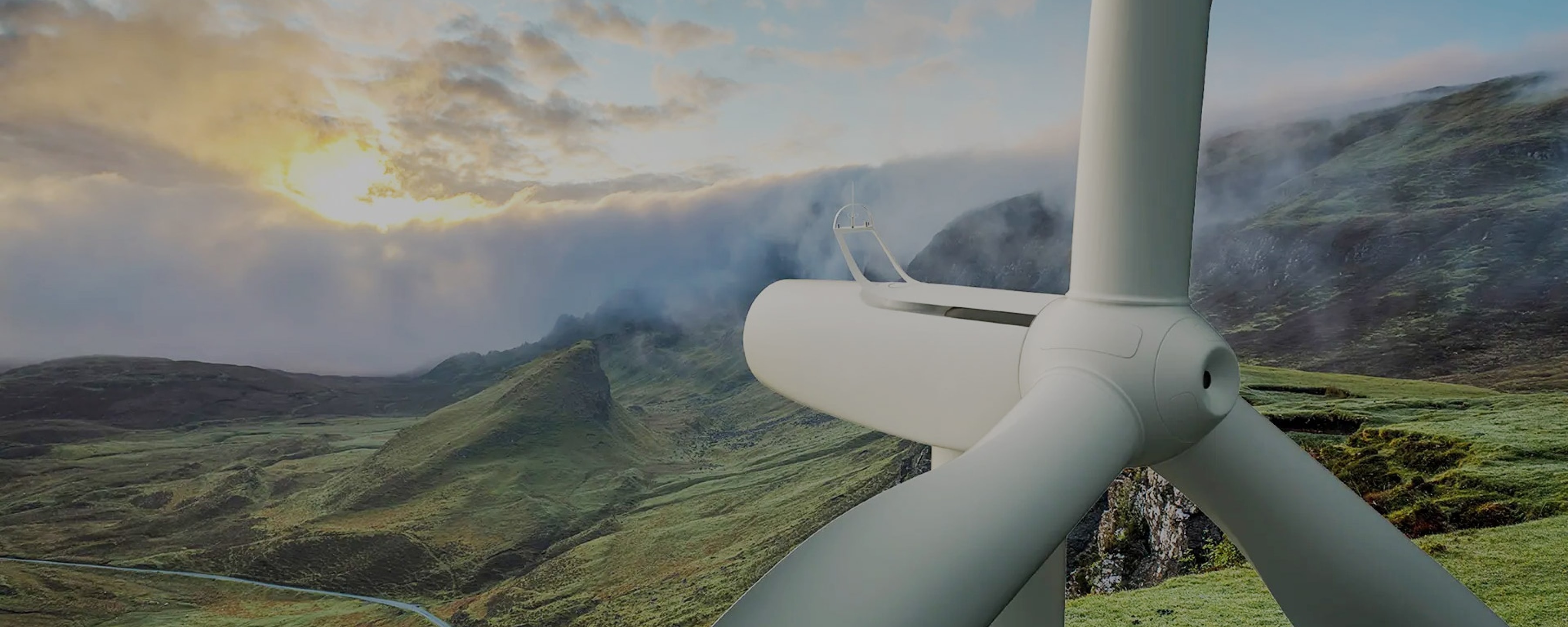
The incorporation of carbon fiber composite materials in wind turbine blades yields multiple advantages: firstly, significantly reducing blade weight diminishes the risk of blade-tower contact; secondly, it enhances wind energy conversion efficiency, allowing wind power generation systems to produce more electricity; lastly, it elevates blade adaptability, enabling stability and efficiency in adverse weather conditions, while offering superior corrosion resistance and adaptability to a wider range of environmental changes.
The incorporation of carbon fiber composite materials in wind turbine blades yields multiple advantages: firstly, significantly reducing blade weight diminishes the risk of blade-tower contact; secondly, it enhances wind energy conversion efficiency, allowing wind power generation systems to produce more electricity; lastly, it elevates blade adaptability, enabling stability and efficiency in adverse weather conditions, while offering superior corrosion resistance and adaptability to a wider range of environmental changes.
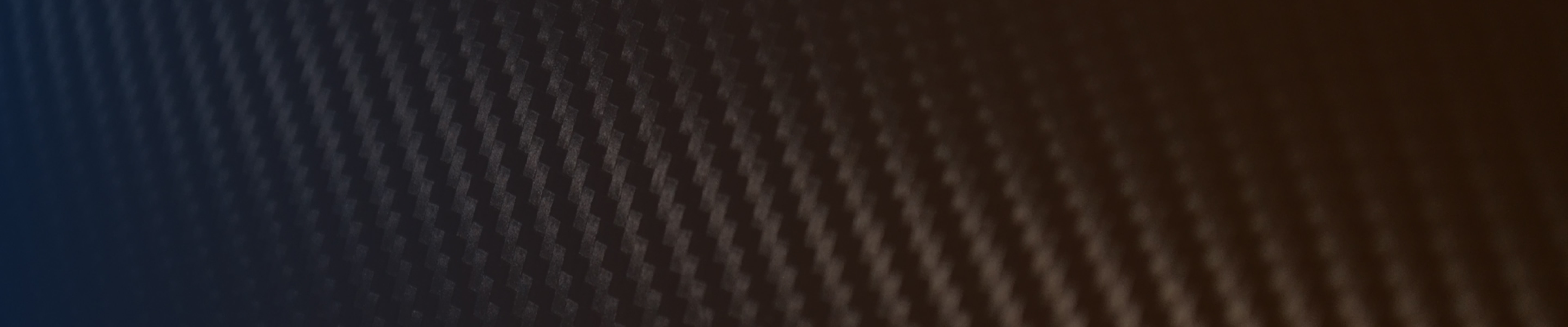
Get In Touch With Us!
To know more about our composite products and solutions, contact our experts! Here is how you can reach us.
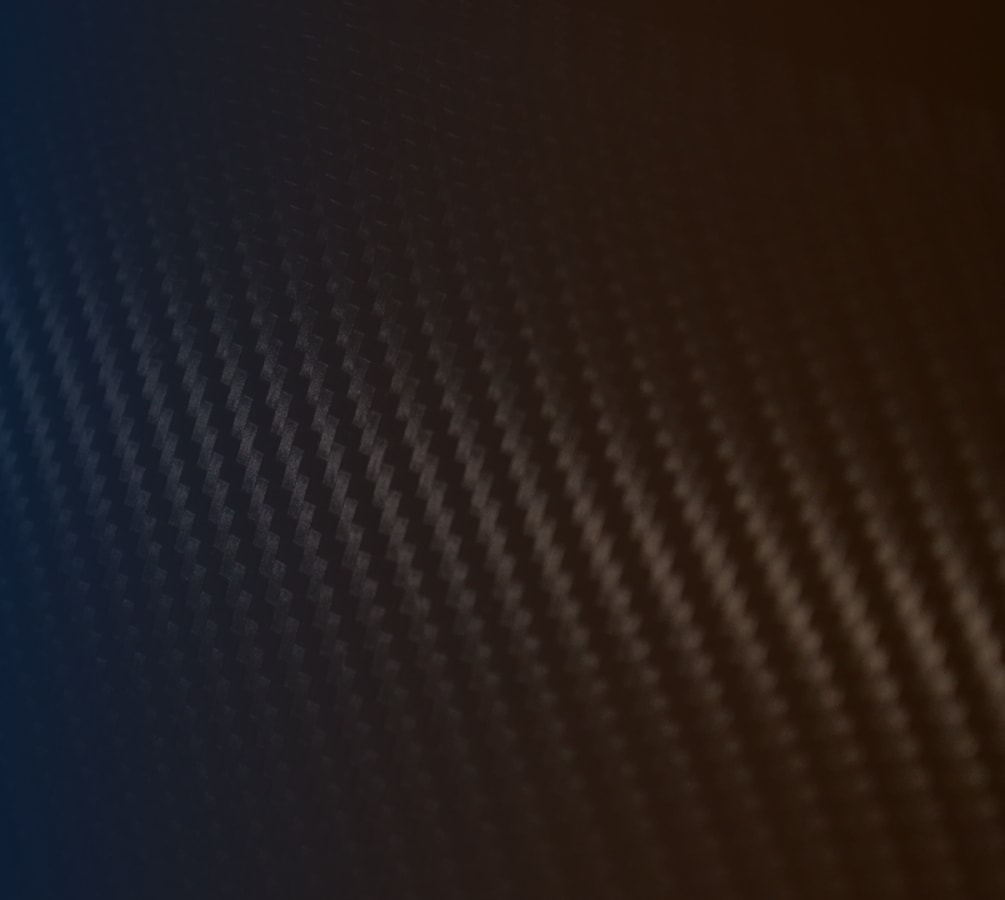
Get In Touch With Us!
To know more about our composite products and solutions, contact our experts! Here is how you can reach us.
Popular Composite Materials
Popular Composite Materials
Related Composite Materials Industries
Related Composite Materials Industries
Composites Knowledge Hub
Composites Knowledge Hub